Spot Welding Machine for Battery: An Essential Tool for Battery Assembly
A spot welding machine is an indispensable tool in the assembly of battery packs, particularly for connecting battery cells to form a unified module. By creating robust and precise welds between cell tabs and connecting plates, spot welding ensures strong electrical conductivity and mechanical stability, which are critical for the performance and longevity of battery packs.
These machines are widely used in the manufacturing of battery packs for electric vehicles (EVs), portable electronics, energy storage systems, and more. Spot welding is especially suited for joining thin metal components, such as nickel strips and battery tabs, due to its precision and minimal thermal impact.
---
● How a Spot Welding Machine Works
Spot welding is a process in which two metal surfaces are joined by applying pressure and heat generated by an electric current at specific contact points.
●# Key Steps in Spot Welding:
1. Preparation:
- The battery cells and connecting materials (e.g., nickel strips) are positioned in the welding fixture. The area to be welded is cleaned to ensure good conductivity and a strong bond.
2. Current Application:
- The welding electrodes press against the metal surfaces to create a strong connection.
- An electric current flows through the electrodes, generating localized heat at the contact point.
3. Weld Formation:
- The heat causes the metals to melt and fuse, forming a solid joint as the material cools.
- Pressure is maintained throughout the cooling phase to ensure a uniform weld.
4. Final Inspection:
- The weld is inspected visually or with testing equipment to ensure it meets quality standards.
---
● Key Features of Spot Welding Machines for Battery Applications
1. Precision Welding:
- Modern machines are equipped with fine control over welding parameters, including current, pulse duration, and electrode pressure, ensuring clean and accurate welds without damaging the battery cells.
2. Programmability:
- Advanced machines allow users to program specific welding sequences and store multiple settings for different battery pack configurations.
3. Adjustable Current Control:
- The ability to adjust the welding current ensures compatibility with a range of materials and thicknesses, from thin nickel strips to thicker busbars.
4. Dual or Multiple Welding Heads:
- Some machines come with dual welding heads, enabling simultaneous welding of multiple points, improving efficiency and throughput.
5. Automatic Alignment Systems:
- High-end machines feature automated alignment for precise positioning of welding electrodes and materials.
6. Compact and Portable Options:
- Bench-top spot welders or portable handheld units are available for small-scale operations or field repairs.
---
● Applications of Spot Welding Machines
1. Battery Pack Assembly:
- Joining individual cells in configurations such as series or parallel to form battery packs.
2. Busbar Welding:
- Attaching busbars to battery cells for large-scale modules, such as in EVs or energy storage systems.
3. Repair and Prototyping:
- Used in repair workshops or R&D labs for creating or modifying small battery packs.
4. Metal Component Joining:
- In addition to battery applications, spot welding machines are often used for joining thin metal sheets or components in electronics and manufacturing.
---
● Types of Spot Welding Machines
1. Manual Spot Welders:
- Ideal for small-scale operations or R&D labs.
- Operated by hand and typically used for prototypes or repairs.
2. Semi-Automatic Spot Welders:
- Require manual placement of materials but automate the welding process itself.
- Suitable for medium-scale production.
3. Fully Automatic Spot Welding Machines:
- Integrates automated material handling and alignment systems.
- Common in large-scale battery pack production lines, such as those for EVs or grid storage.
4. Portable Spot Welders:
- Handheld devices designed for on-site repairs or low-volume welding tasks.
---
● Key Materials and Considerations
1. Nickel Strips:
- Nickel is commonly used for connecting battery cells due to its excellent electrical conductivity and resistance to corrosion.
2. Copper Busbars:
- Copper is often used for high-power applications but requires specialized machines capable of welding thicker materials.
3. Electrode Material:
- Spot welding electrodes are typically made of copper alloys to ensure good thermal and electrical conductivity.
4. Battery Safety:
- Care must be taken to avoid overheating the battery cells during welding, which could damage the internal chemistry or cause safety issues.
5. Weld Strength:
- The weld must be strong enough to maintain a solid electrical connection while withstanding mechanical stresses, such as vibration or thermal expansion.
---
● Advantages of Spot Welding Machines
1. Speed and Efficiency:
- Spot welding is a fast process, ideal for high-throughput production lines.
2. Reliability:
- Produces consistent welds with minimal variability, ensuring uniform quality across all battery packs.
3. Cost-Effectiveness:
- Spot welding is more economical than other joining methods, such as soldering, especially for large-scale production.
4. Minimal Heat Damage:
- The localized heating ensures that only the contact points are affected, preserving the integrity of the surrounding materials.
---
● Challenges in Spot Welding for Batteries
1. Material Compatibility:
- Joining dissimilar materials, such as copper and nickel, can be challenging and may require specialized equipment.
2. Thin Material Welding:
- Welding very thin materials without creating burn-through or excessive deformation requires precise control over welding parameters.
3. Battery Safety:
- Overheating during welding can damage battery cells or cause internal short circuits, necessitating careful parameter optimization.
---
● Spot Welding Standards
- UN 38.3: Safety standards for lithium-ion batteries, which include guidelines for manufacturing and testing.
- ISO 18278: International standards for resistance welding, including spot welding.
---
● Conclusion
A spot welding machine is an essential tool for the assembly of battery packs, providing a reliable, efficient, and cost-effective method to join battery cells and components. With advancements in automation and precision, spot welding machines have become indispensable in industries like electric vehicles, consumer electronics, and renewable energy storage. By ensuring robust and high-quality welds, these machines contribute to the overall safety, performance, and longevity of modern battery systems.
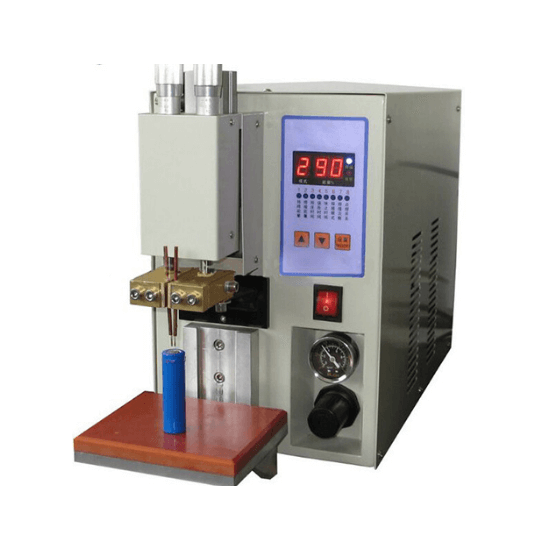